HK-4035 Build and Review (by Dr. Ralph Okon, AKA PowerCroco)
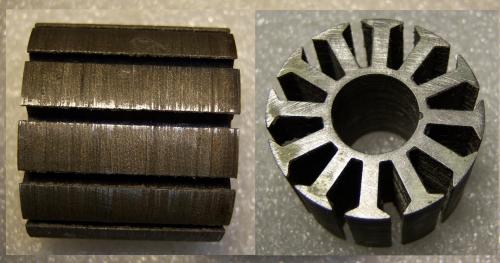
This is the biggest of the scorpion kits.
You will find some real innovations in it compared to the other kits.
The kit includes all needed parts and materials without magnet wire and glue.
The parts all have really high quality, how I found it just into this kit.
The foto shows the most important part -the 35mm high statorpackage made from 0,2mm plates in the newer "G2" shape. The diameter is 40mm.
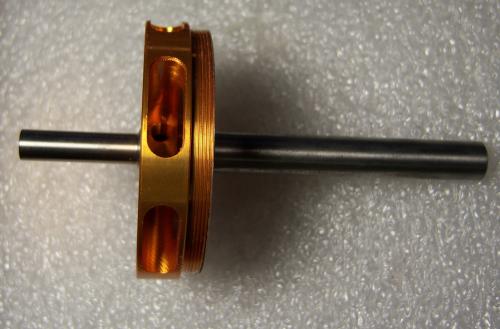
The fine grinded 8/6mm shaft into the as radial-fan working can bottom.
You can see the metric thread for the perfect connection between can bottom and backiron.

The thick and very stabil shaft runs into fat 688 ZZ bearings (16x8x5mm).
The bearing thought for the statorholder side fits direct into the hole of the statorpackage.
This is a by other manufacturers too used method to bring in a really fat bearing to there.
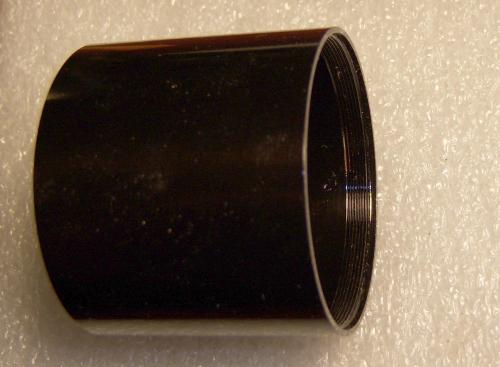
The backiron is 1,5 thick.
You can see the counterpart of the metric thread here.
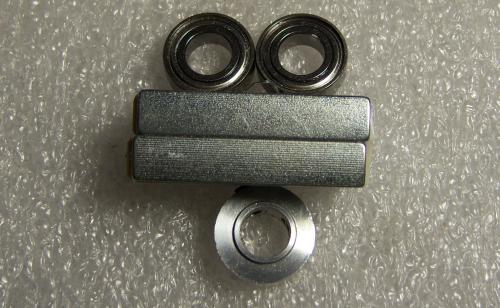
The bearings, the stopring and 2 of the 35mm long and 2,5mm thick segmentmagnets.
These magnets are rated as N 50EH - good for tempatures up to 200°C.
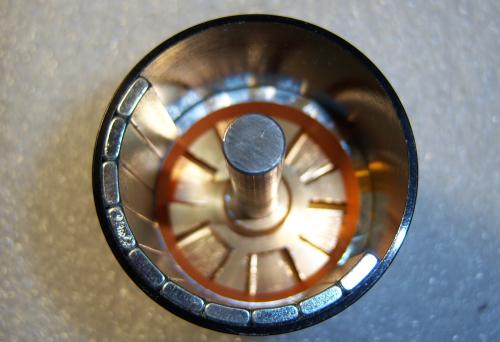
The magnets into the screwd and glued can.
Coverage is only about 50%.
This made me sceptical (a bit less for my mind) but have a look on data at the end of this page...... They are absolutly convincing.
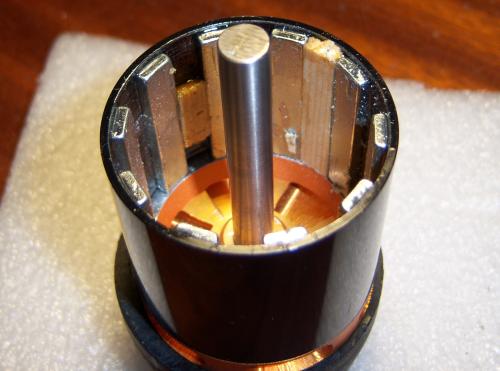
I placed the magnets using wooden parts for help.
I glued them with a 200°C rated 2-component gluing system. You can also use loctite 638 or 648 to get a high resilent connection.
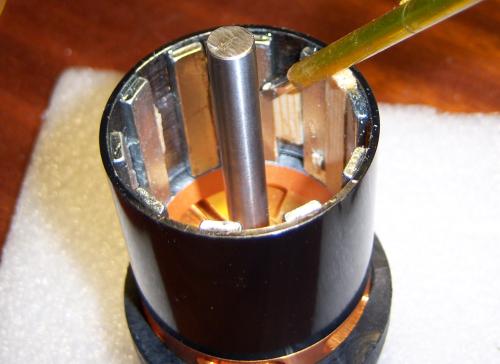
After gluing I removed the wood.
If you have a good glue, its better to do so: the free spaces works air cooling air channels trough the motor.
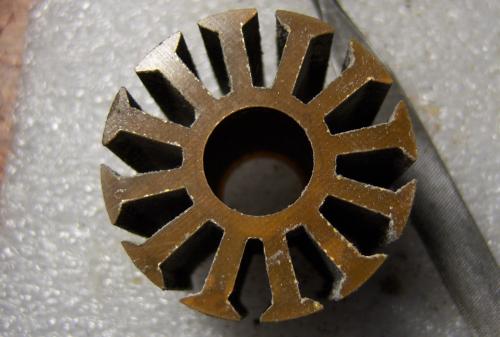
In the kit don't included epoxi endplates yet. I use this way to improve the insulation only by paper into the slots.

The 0,15mm insulation paper is rated for 200°C temperature too. I glued it with acryl-cyanate-glue into the slots.
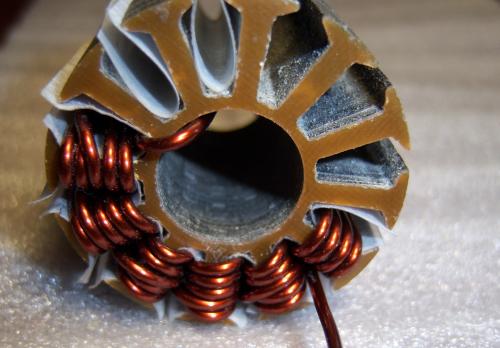
Winding is made in small groups and using the zick-zack mode for the last turn.
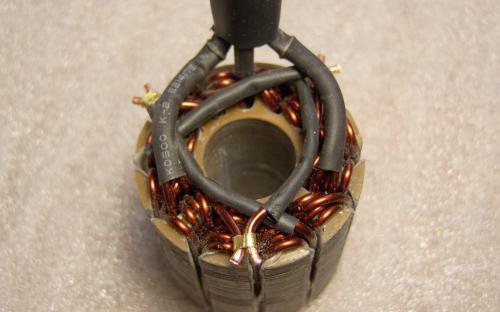
This is a delta winding befor esoldering the connection wires.
I used 5turns 1,5mm wire here.
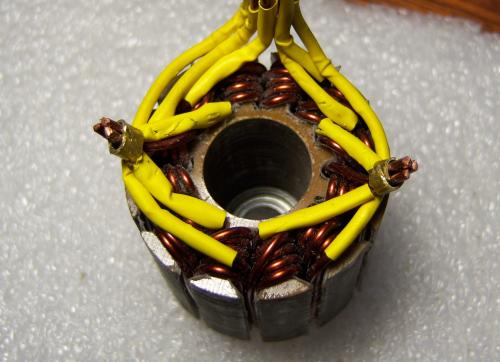
This is a 6turns 1,4mm wire group-parallel WYE winding.
Details about this kind of winding you can find here.
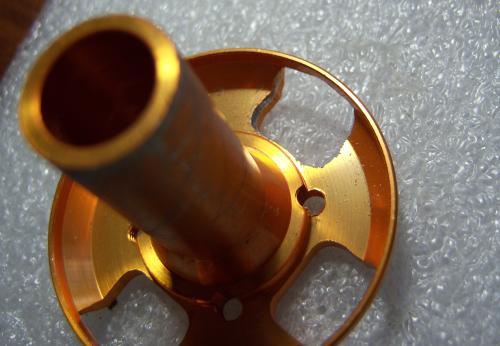
You should break the edges into the wire leading hole of statorholder to prevent short in the future..
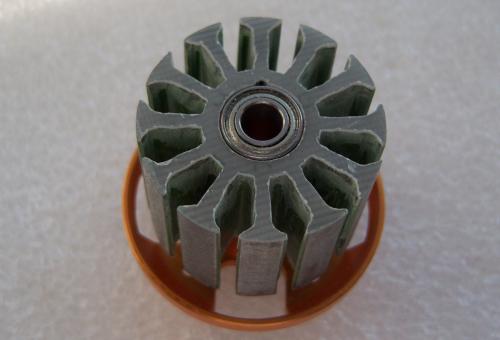
The frontside bearing fits direct into the statorhole.
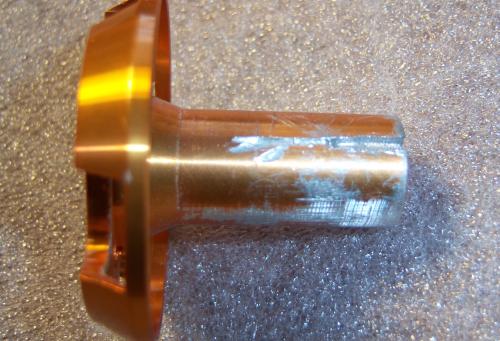
I cut a screw saving channel into the statorholder.
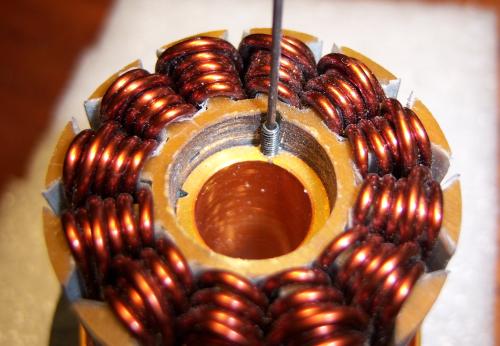
I cut a M2 thread between package and holder and put a screw in it.
But if you don't need a removeable connection, you also can glue the package on the holder! but in this case you should not abdicate on the screw saving- a wire into a cut/ bored channel will do the job!
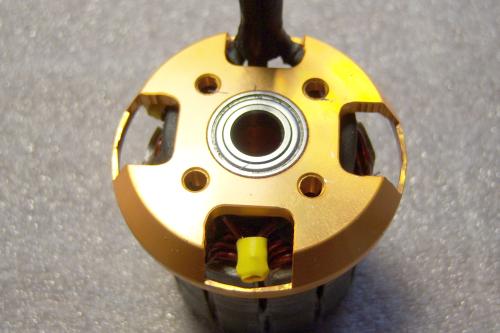
The last bearing is placed too.
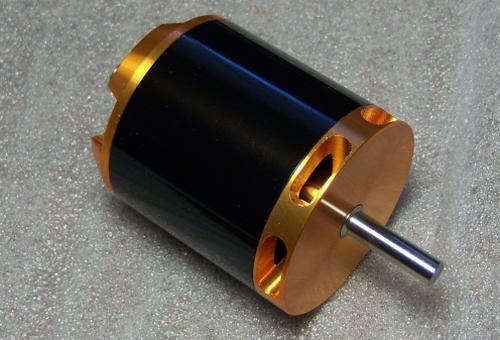
The ready built motor.
Its weight is 400-430g - depending on the used amount of copper in it.
Some lad- data for several windings.
2 of these windings are made for 6S batttery and big airscrews, one for 10-12s battery for big heli drive.
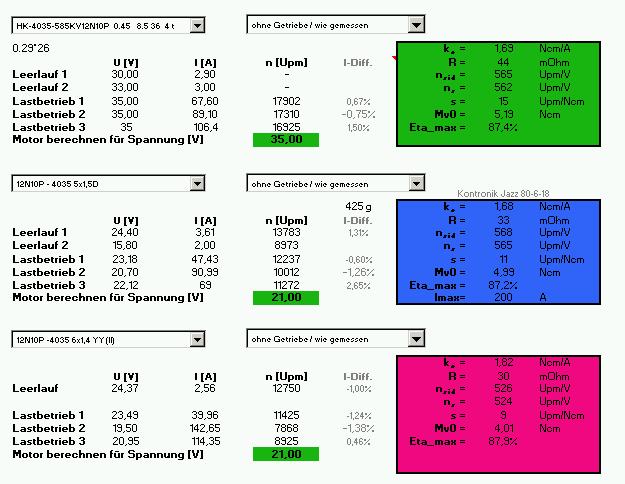
The data shown as diagram. I like these curves!
The thick shaft and strong bearings seems good enough to hold the strong forces of this really long built motor.
But I'am not sure, if this si strong enough to resist the circular forces into acrobatic flight.
Sure,someone will test this into the future.
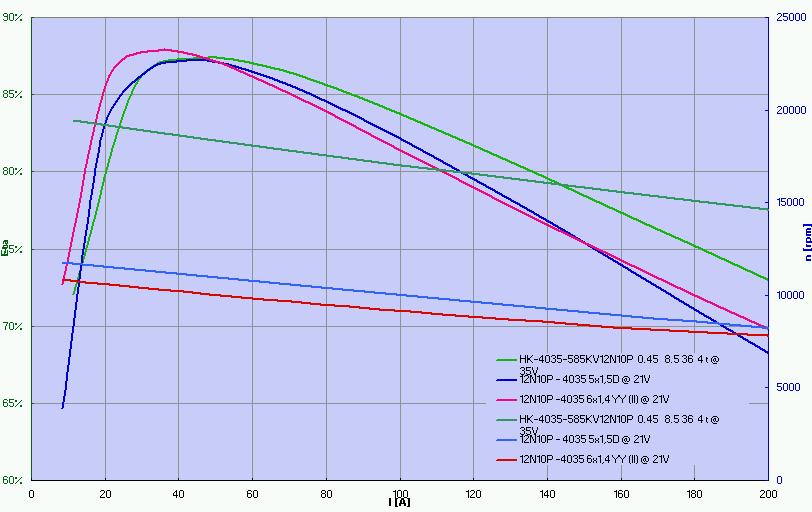
My conclusion:
- a real powerhouse for a wide range of use.
- very good mechanics with very interesting detail solutions.
- the kits are very good usable for customizing as shown here with another statorshape and shortened housing.
- and I like the load data of this motor!